Seamless pipes are used in various industries, including oil and gas, construction, and automotive, due to their high strength and ability to withstand extreme conditions. The manufacturing process of seamless pipes involves several stages, including post-processing, which is crucial for ensuring the quality and performance of the pipes. Here's an overview of the process and purpose of seamless pipe post-processing:
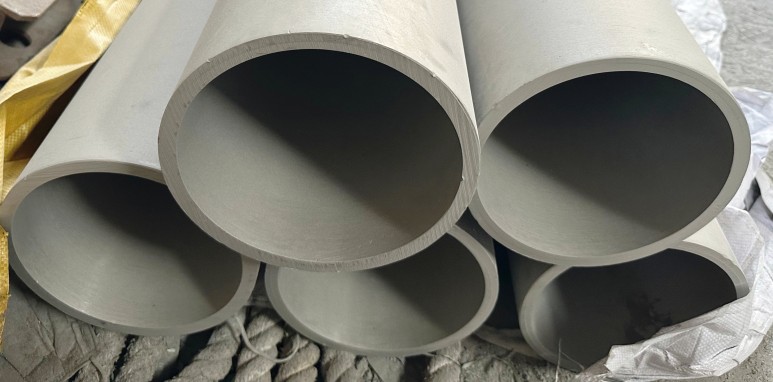
Process of Seamless Pipe Post-Processing
Heat Treatment:
- Purpose: To relieve stresses induced during manufacturing, improve mechanical properties, and refine the grain structure.
- Types: Common methods include annealing, normalizing, quenching, and tempering.
- Annealing: Heats the pipe to a specific temperature and then slowly cools it to make it more ductile and reduce hardness.
- Normalizing: Heats the pipe above the critical temperature and then air cools it to achieve a uniform grain structure.
- Quenching and Tempering: Involves rapid cooling (quenching) followed by reheating (tempering) to achieve desired strength and toughness.
Descaling:
- Purpose: To remove scale and oxide layers formed on the surface during the heating process.
- Methods: Common techniques include acid pickling and mechanical descaling (e.g., shot blasting).
Straightening:
- Purpose: To ensure the pipe is straight and meets specified dimensional tolerances.
- Methods: Pipes are passed through a series of straightening rollers or machines.
Non-Destructive Testing (NDT):
- Purpose: To detect surface and internal defects without damaging the pipe.
- Methods: Includes ultrasonic testing, eddy current testing, magnetic particle inspection, and radiographic testing.
Hydrostatic Testing:
- Purpose: To test the pipe’s ability to withstand pressure and ensure there are no leaks.
- Process: The pipe is filled with water and pressurized to a level higher than its operating pressure.
Finishing:
- Purpose: To improve the surface quality and dimensions of the pipe.
- Methods: Includes processes like grinding, polishing, and coating (e.g., galvanizing or painting).
Cutting and Beveling:
- Purpose: To cut the pipes to specified lengths and prepare the ends for welding.
- Methods: Cutting can be done using saws, torches, or laser cutters, while beveling is done using specialized machines to create an angled edge.
Marking and Packaging:
- Purpose: To identify the pipes and protect them during transportation.
- Process: Pipes are marked with essential information (e.g., size, grade, manufacturer) and then packed using methods that prevent damage (e.g., bundling, wrapping).
Purpose of Seamless Pipe Post-Processing
Enhancing Mechanical Properties:
- Processes like heat treatment improve the strength, toughness, and ductility of the pipes, making them suitable for demanding applications.
Ensuring Dimensional Accuracy:
- Straightening, finishing, and cutting processes ensure that the pipes meet precise dimensional specifications, which is critical for their proper installation and performance.
Surface Quality Improvement:
- Descaling and finishing processes ensure a smooth surface, reducing the risk of corrosion and facilitating easier inspection and maintenance.
Defect Detection and Prevention:
- Non-destructive testing and hydrostatic testing help identify defects early, ensuring that only high-quality pipes are delivered to customers.
Compliance with Standards:
- Post-processing ensures that the pipes meet industry standards and regulations, which is essential for safety and reliability in their intended applications.
Preparation for Use:
- Cutting, beveling, and marking prepare the pipes for immediate use or further fabrication, making installation quicker and easier.
In summary, post-processing of seamless pipes is a vital series of steps aimed at improving the physical and mechanical properties of the pipes, ensuring their quality and compliance with standards, and preparing them for their final application.